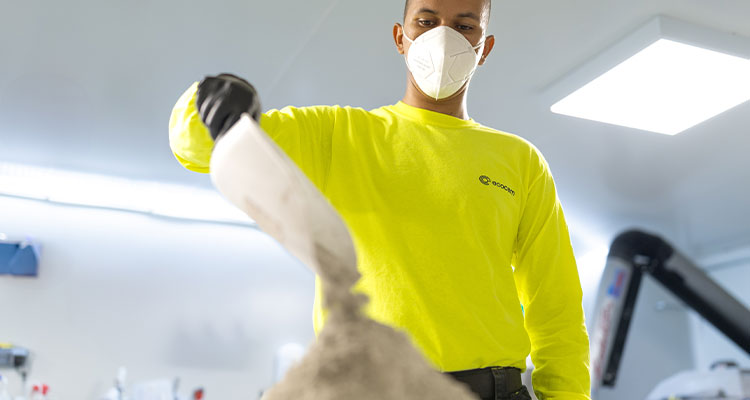
The key to spurring a US construction boom: efficient, low carbon cement production
In recent years, high mortgage and interest rates and a slowdown in housing starts – the number of new residential projects initiated annually – have weakened cement demand in the US. At the same time, rising prices, driven by high energy costs and supply chain constraints, have worsened the situation, marking 2024 as the worst year since 2017 in cement production volume. As a result, the US has entered a cement recession and deficit, now relying on foreign imports for approximately 25 percent of its cement supply.
While attention shifts to the possibility that the cement deficit may become more expensive as the US takes a harder line on global import tariffs, we can’t forget that cement production is a major contributor to carbon emissions – responsible for almost eight percent globally. Fortunately, a new generation of low-carbon cement technologies offers new ways to use existing resources more effectively while significantly reducing emissions by up to 70 percent. These solutions allow the industry to expand without sacrificing sustainability or affordability, and without major changes to existing manufacturing processes.
Creating a competitive edge
With construction activity expected to be burdened by increasingly high interest rates in the short term and US demand for cement continuing to fluctuate, the industry faces a critical need to evolve beyond traditional production methods – methods that have remained unchanged for many years now, unlike in Europe, where advanced cement technologies are already in use.
These methods use materials with much greater efficiency; they are cost-competitive and deliver the required performance in terms of durability, workability and strength in any concrete they are used to make. They also significantly reduce CO2 emissions during the manufacturing process.
European countries have been actively implementing new low-carbon cement technologies across multiple countries for years, while the US is just starting to experiment. For example, Ecocem, Europe’s leading provider of low-carbon cement technologies, has been deploying low-carbon cement used in a range of major European infrastructure projects from Le Grand Paris Express to Dublin’s Aviva Stadium, the UK’s high-speed railway HS2 and the athletes’ village in Paris. Using this low-carbon technology, Ecocem has prevented almost 18 million tons of CO2 emissions.
While just beginning to scratch the surface, there’s an opportunity for US construction companies to also adopt low-carbon cement technologies to create a competitive advantage. The global business community increasingly demands low-carbon solutions for managing their carbon footprint, and next-generation cement can meet these demands without additional costs or operational changes.
Leveraging readily available materials to reduce energy use and emissions
One of the most significant opportunities for cutting emissions in cement manufacturing is reducing reliance on clinker, which accounts for 90 percent of its emissions. The use of Supplementary Cementitious Materials (SCMs) also reduces the amount of energy required in cement production, contributing to lower CO2 emissions and operating costs. As the Rocky Mountain Institute points out, cement and concrete producers can use a variety of SCMs to replace clinker and lower embodied carbon while still crucially meeting specifications. Historically, these SCMs have included:
- waste or by-product pozzolans, such as fly ash and ground glass, which are mostly silica,
- natural pozzolans, such as volcanic ash, which perform similarly to waste pozzolans, and
- ground granulated blast furnace slag (GGBFS), a by-product of steelmaking that contains calcium and silica and that can almost entirely replace Portland cement.
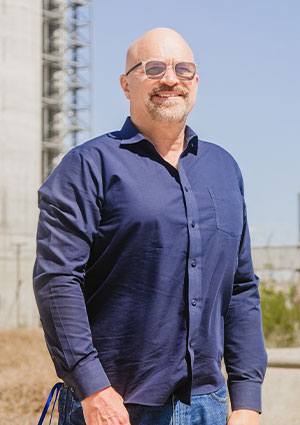
Alternatively, the most-used clinker substitute in Ecocem’s ACT technology is limestone, one of the world’s most abundant materials, making wide-scale adoption across North America not only feasible, but easy. With the US already somewhat familiar with SCMs, the industry has a foundation for wider adoption of low-carbon cement without major disruptions to manufacturing plants or construction processes. It’s worth noting that while this alters the composition of the cement, alternative low-carbon options can provide the same strength and performance as traditional cement.
Maintaining cost-competitiveness and high-performance
Industries can face a ‘green premium’ when adopting sustainable solutions. However, low-carbon cement developed with SCMs is an exception – it is cost-competitive and, in some cases, even cheaper than traditional Portland cement, according to The Rocky Mountain Institute. Research has demonstrated that SCMs can lower costs in multiple ways. They are often cheaper than traditional clinker, especially in areas where they are locally available and they improve workability and durability, reducing the total cement required in construction projects. And, in the same way that SCMs offer performance benefits through efficiency, this translates to lower material costs because it requires less energy to produce when compared with the same volume of clinker. To understand how this would look in practice, Ecocem’s ACT technology uses existing resources more efficiently and can do more with less, reducing emissions by up to 70 percent. For construction companies, low-carbon cement can be a practical, cost-effective solution that supports sustainability goals without added cost.
The bottom line is that concrete is the most consumed man-made material in the world and that isn’t going to change. The US alone is estimated to have consumed 120 million metric tons in 2023, and that number is only set to grow. As such, the nation’s reliance on imported cement and energy-intensive clinker production threatens to create economic and environmental challenges as demand rises. It’s essential to understand that addressing cement emissions does not have to come at the cost of business; low-carbon cement is a strong foundation for building innovative industries and economic growth.
The reality is that some will look to low-carbon cement for sustainability reasons, while the majority will remain focused on affordability. With cost-competitive solutions that have the potential to become cheaper than conventional concrete in being more efficient to produce available today, the industry can expand while reducing emissions, cutting costs, and maintaining performance.
For a list of the sources used in this article, please contact the editor.
Steve Bryan
Steve Bryan is Managing Director at Ecocem. Ecocem is a pioneer in high-performance technologies that significantly reduce CO2 emissions in the cement and construction sectors. Its innovative ACT technology reduces the overall carbon footprint of traditional cement manufacturing by over 70 percent. For more than 20 years, Ecocem has developed, manufactured, and supplied low-carbon cement and construction solutions across European markets.