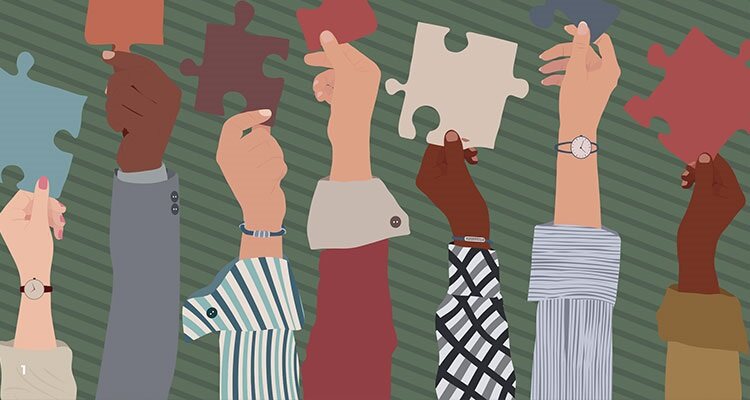
In every construction project, collaboration is essential, according to CEO Scott Gebicke. He discusses how the difference between innovation and stagnation in construction depends on how we collaborate
In the realm of construction, ‘collaboration’ is not just a buzzword. From small homes to towering skyscrapers, no structure comes to life without the synchronized efforts of contractors, subs, architects, suppliers, developers, lenders, and municipalities – each with their unique approach, and each project with specific requirements. In many respects, the coordination required for any project is a small miracle. But the need for such extraordinary synchronization can also be the industry’s most formidable barriers to innovation. In an environment where capital is hard to come by, margins are slim, and you’re lucky if you have access to reliable skilled work, it’s much easier to fear a big loss than to reimagine the foundations of how we work together to build better.
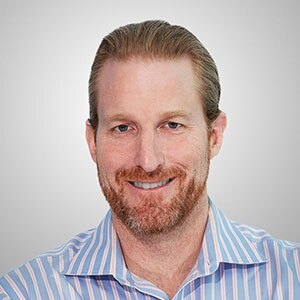
At Mighty Buildings, we’re tackling construction inefficiency by focusing on a critical element: walls. With an outsized impact on structural integrity, energy efficiency, material usage, and trade scheduling, walls heavily impact the speed, sustainability, and cost-effectiveness of projects. So we use material science and 3D printing to manufacture panelized kits, known as the Mighty Kit System (MKS), that help our partners build more resilient homes faster.
But the envelope is just one piece of a building, so how can we seamlessly integrate our technology with existing processes, components, and systems to ensure an entire project is improved? The question for us isn’t if we should collaborate; it’s how, when, and with whom?
Consider any home or building. Our wall panel system features clear rules and standard details for interfacing with, for example, windows and doors. We have options for sealants between panels, varying panel sizes (height, width), and different exterior surface appearances (parametric panels) to make adoption and execution as easy as possible. But ultimately, the engineer and architect carry the liability for their particular building, the vision for exactly what the building will look like, and responsibility for delivering a finished product to the customer. If they want to incorporate a particular window product or unique detailing, we need to account for it. That requires early coordination with multiple stakeholders. And of course, this is not just true for windows and doors, but for all aspects of the building, from the structural system to MEP to wind loading and fire rating requirements.
A recent project with the Buckminster Fuller Center provides an illustrative example. Our customer wanted to use our system to build a Visitors’ Center that would sit next to the original historic dome, and feature parametrically designed panels that would nod to the geodesic dome’s unique triangulated pattern. Our approach shifts the bulk of collaboration to the pre-construction phase. We collaborated early and often with the client and designers of record, external contractors, roof, and windows suppliers, as well as our own internal design, manufacturing and supply chain teams. In a matter of hours, we translated our client’s designs into our system, schematically determining panel layouts, locations, and sizes of structural members. And then we coordinated with the client to ensure the adapted design met their needs, ultimately saving weeks of work onsite. Much of this is enabled by digital collaboration tools: we use Autodesk Construction Cloud (ACC) and Revit blocks, we meet constantly via Zoom to review, and we scan the site with Matterport as we progress through each phase.
The result is that we needed significantly less collaboration when the project was in its riskiest phase – onsite construction. On a uniquely designed project for a historic landmark, we assembled all structural components and 3D-printed panels in four days, with a team of three, no special equipment, zero RFIs, and absolutely no deviation from plans. The point isn’t that every project should be unique. It’s that for better or worse each project is unique and requires significant collaboration. But if you frontload that collaboration and use configurable building systems with clear logic, you’ll lower both the total amount of time you need to coordinate, as well as your risk exposure.
The industry’s broader challenges mirror those in individual projects, as do its solutions. We need concerted effort from governments, industry bodies, and civil society organizations to incentivize collaboration before projects begin. We need to develop sensible building standards that align a variety of methodologies into unified code, even though it will take upfront compromise. We need to incubate novel technologies alongside trades, developers, and municipal partners to ensure good ideas don’t die in isolation. And we need funding that brings diverse parties together to address some of our most intractable challenges.
The California Energy Commission has recently taken a step in the right direction, introducing grants for groups that partner to develop, test, and demonstrate zero-carbon, cost-effective, modular homes. This initiative ultimately brought together disparate entities – Mighty Buildings, Lawrence Berkeley National Lab, and Habitat for Humanity – to generate novel manufacturing, training, and energy solutions that would have otherwise been impossible to execute in the course of a typical project. Only by demonstrating the impact of these techniques in real buildings, for real people, can we de-risk such approaches and pave a new path for collaborative methods.
Looking ahead, it’s clear that the future of construction hinges on more than just technical innovation. It requires a fundamental shift in how we approach projects, emphasizing collaborative methods from the outset. This change isn’t just beneficial; it’s necessary for an industry facing global challenges like housing shortages and climate change.
Scott Gebicke
www.mightybuildings.com
Scott Gebicke has held several leadership roles at Jabil over 11 years, including President of the Industrial Division and of Jabil Defense & Aerospace. He is a veteran US Naval Officer and previously was a leader in McKinsey & Company’s industrial practice, supporting high tech clients across areas including growth, innovation, and operational turnouts. Now, as CEO of Mighty Buildings, he is focused on driving adoption of Mighty Buildings’ 3D-printed net-zero energy homes, which leverage green materials, innovative design and automated precision, to address sustainability, climate resiliency and housing shortage issues in the US and worldwide.