How modern ConTech tools increase safety on construction job sites
When construction executives sit down to develop plans, bids, and schedules for a project, profitability and efficiency are always top of mind. However, worker safety is another extremely important element that contributes directly to a company’s success and reputation, as well as the health and wellbeing of their employees.
According to the Bureau of Labor and Statistics, the construction industry is the most dangerous industry. With fatal work injuries outpacing other industry sectors, maintaining worker safety is indisputably one of the most important concerns for construction teams. To mitigate the on-site risk and protect their workers, construction company leaders have had to identify and implement new tools and practices to ensure that safety is a top priority from the very beginning to the very end of a project while also prioritizing timeliness, efficiency, and profitability.
Ongoing obstacles standing in the way of safety
Today, construction firms face numerous challenges that impact both the successful completion of projects and the safety of workers on site. These include labor
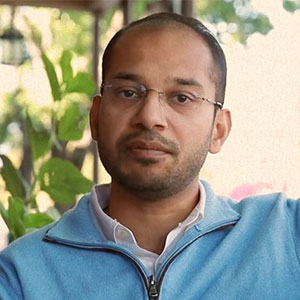
shortages, supply chain delays, rising material costs, and inclement weather conditions. In addition to hindering contractors’ ability to maintain efficient and profitable operations, these challenges also directly impact the safety of their workers, both directly and indirectly, which is debatably the most important part of a job.
One of the largest concerns facing the construction industry over the last several years has been the ongoing shortage of skilled laborers. As growing numbers of the construction workforce approach retirement age and prepare to leave the industry, construction companies are struggling to keep pace with the continued momentum of projects because the individuals leaving these jobs are not being replaced by a new, younger group of workers. These staffing concerns have led to teams that are spread too thin and often overworked to complete tasks in the allotted time frames. Furthermore, it is extremely difficult to prepare for unexpected events that cause project delays or additional work because these companies are already inadequately staffed.
Additionally, inclement weather conditions including heavy rain, snow, sleet, frigid and exceedingly high temperatures, high winds, hurricanes, tornadoes, wildfires, and more create hazards that threaten job site safety. In addition to causing disruptions in the project momentum, these events impact visibility on job sites and create barriers to the production of quality work, delaying processes until further notice.
Supply chain delays and ongoing increases in material costs have also placed more pressure on construction teams and impacted worker safety. Both factors are actually closely tied to inclement weather, as the market changes depending on the ability to acquire and ship materials. For example, droughts or flooding that occur near major shipping routes can result in delivery delays and an increase in prices, which in turn can place increased pressure on budgets and make it difficult for contractors to hire more employees when necessary. Consequently, this can result in smaller teams of overburdened workers who are expected to work extra hours and take on tasks that they may not be properly trained to do, which puts their safety at risk.
When left unaddressed, these obstacles can snowball into dangerous incidents and large issues that can result in workplace injuries, delayed projects, and in some cases, reputation damage that can haunt an organization for years to come.
Leveraging ConTech to optimize schedules and prioritize worker safety
Although so many factors are out of the direct control of contractors, modernizing ConTech to optimize workflows and the way they plan, and schedule projects can help prioritize worker safety. With strategic implementation, new digital construction technology can help contractors solve a multitude of problems. Thanks to recent developments in these technologies, project schedules have evolved far beyond a simple timeline of tasks. Now, they can be used as an effective tool to manage safety risks on job sites. The capabilities new technology provides enables teams to develop comprehensive plans that also boost visibility into complex projects.
In addition to increased visibility and safety, benefits of new ConTech solutions include course correction, a single source of truth, and a better, more intuitive dashboard that makes it easy for teams to analyze important data to fine-tune scheduling and planning efforts. This allows teams to create, analyze, and update schedules to reflect changes in plans while also adhering to important safety guidelines.
When properly optimized with new ConTech, construction schedules can facilitate strategic planning, sequence tasks, allocate resources, and more. As a result, teams can identify and reduce safety risks on job sites, protecting both employees and a company’s overall success.
Real world application
A recent case study from R&H Construction, one of the largest commercial construction companies in the Northwest, highlighted that the use of a new scheduling solution resulted in the ability to consistently produce 25 percent higher quality pre-construction schedules as well as a significant improvement in job site safety. By investing in new ConTech that allows them to rethink the processes needed to manage an increasingly complex workflow of contractors, subcontractors, engineers, inspectors, and more, R&H has tackled a daunting task that many construction companies have yet to approach. This differs from many other contractors who still take an extremely low-tech approach to the problem, relying on overly simplistic, paper-based management processes despite major tech advances.
By taking a higher-tech approach to scheduling, R&H now has the technology in place to more effectively collaborate with the Environmental Health & Safety department to tag, identify, and break down the high-hazard activities on the site to determine the right level of support needed. This allows the construction team to properly staff and prepare for potential safety issues, including fall protection, and prioritize the safety of their workers.
By Nitin Bhandari
Nitin Bhandari is CEO and Co-Founder of Planera, a full CPM-based scheduling and planning platform for the construction industry. With an innovative 3D whiteboard, Planera enables all stakeholders to create, review, and optimize schedules. Planera addresses scheduling needs in all three phases: pursuit, pre-construction, and project execution. Advanced features like built-in schedule quality audit and Monte Carlo risk simulation set Planera apart from other legacy CPM scheduling software.