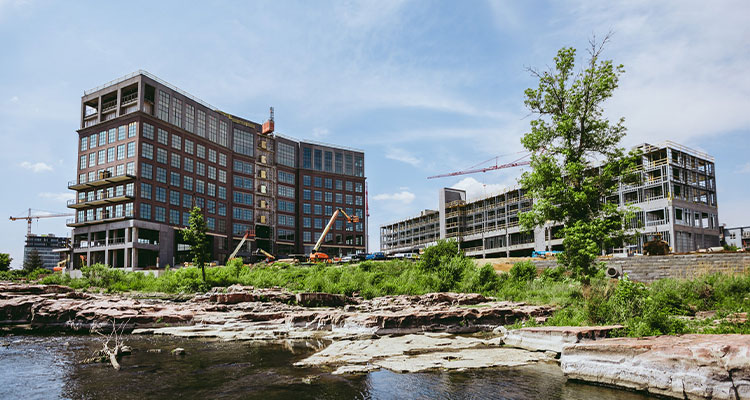
Gage Brothers makes waves in the industry by championing diversity and Ultra-High Performance Concrete
Leading the way in quality precast concrete solutions, Gage Brothers (Gage) builds beautiful communities and structures supporting the places people visit, learn, work, and play. The company specializes in architectural precast, structural precast, Ultra-High Performance Concrete (UHPC), total precast solutions, design assistance, and caulking services. To learn more about Gage’s background and place in the industry, we have the pleasure of speaking with Joe Bunkers, CEO.
“For over a century, our core operations have consisted in pouring concrete in Sioux Falls, South Dakota. In the 1940s, when the Gage brothers returned from the war, we incorporated precast to our services. From there, we added more products and services to our portfolio to become the company we are today. Currently, we have approximately 275 employees in our Sioux Falls production plant and run a caulking business in Minneapolis and Saint Paul, Minnesota. It is worth noting that though we do not invent our own technologies, we have always been early adopters of technology, rapidly implementing it into our repertoire and deploying it to the market,” he states.
Its early adoption of technology is one of the factors that make Gage stand out from competitors in the market, as Joe points out: “Fear of the unknown does not keep us from moving forward as we embrace new technology and find creative ways for our customers and end-users to incorporate it into their projects. Furthermore, our state-of-the-art plant boosts operational efficiency and allows us to employ a wider variety of people. Traditionally, the construction industry has predominantly attracted male workers due to its physically demanding nature. However, we intentionally engineered much of the hard physical labor out of our production processes, resulting in over 15 percent of our labor force being women. This means that we can employ individuals of varying physical abilities, enabling everyone to find their place and contribute effectively. It also helps us attract and retain a broader range of talent.”
Delving further on the topic, Joe reveals how Gage celebrates diversity in the workplace. “When we built our plant, not only did we deliberately streamline some of the laborious tasks so that more people could work with us, but we also installed separate locker rooms for men and women, each accompanied by a set of restrooms and amenities. To ensure that every single employee – regardless of their gender, nationality, or ethnic background – feels welcomed at Gage, we have hung flags in our break room representing their identity or countries of origin. These flags include those of LGBTQ and transgender pride, the four military branches, and three South Dakota Native American tribes. This serves as a testament to our commitment to inclusivity and ensuring that everyone who comes to work with us know that they fully belong here,” he reveals.
Ambitious project
Recently, Gage received an award for being the first company to use UHPC in a commercial building in the US. “As we did not invent the UHPC mix ourselves and used a nonproprietary mix from the Precast/Prestressed Concrete Institute (which we helped develop and test) instead, the real innovation lay in having the courage to present it as an option to our clients. This decision stemmed from the volatile condition of the steel market at the height of the pandemic, with extremely unstable prices and uncertain availability. Consequently, our contractor developer, whom we have been working with for around 40 years, could not know when they would receive the steel or how much it would cost. To address this issue, we suggested using UHPC for the project, thus taking all the steel out of the building and offering a guaranteed maximum price.
“In the year leading to our formal involvement in the project, we had already started working on it in the background and developed some designs. Once the contractor developer decided to take this leap of faith with us, we assumed Structural Engineer of Record responsibilities to facilitate the transition. We collaborated with the architect, who also agreed to redesign the building, to deliver a nine-story total precast system using UHPC for the 70-foot beams and eliminating all the interior columns,” Joe adds.
The versatility of UHPC is further exemplified by Gage in the construction of tornado-resistant buildings. “We are working on ICC 500 (Standard for the Design and Construction of Storm Shelters) projects designed to resist severe tornadoes in Tornado Alley, especially around Iowa. As part of this, we are developing an ICC 500-rated gym box made of UHPC for schools to provide a safe room large enough to accommodate all students and faculty during emergencies. We truly believe that transitioning to UHPC is more environmentally friendly, as it requires much less concrete not only in the construction of precast elements but also in footings, foundations, and support structures. It also gives the flexibility to repurpose the space in the future without the constraints of columns or other impediments, offering a clean slate to completely change the space, whether in five or 20 years,” Joe concludes.
By promoting diversity and the use of innovative materials like UHPC, Gage is poised to leave a lasting impact on its communities and on the construction industry.